SUSTAINABILITY
Aluminium is central to a sustainable future because of its unique properties including lightness, strength, durability – and infinite recyclability.
In New Zealand, our industry manufactures some of the lowest-carbon aluminium extrusions in the world. This is because our members source most of the virgin aluminium from the New Zealand Aluminium Smelter, powered by renewable energy, or they use recycled aluminium.
New Zealand-produced aluminium has smelting emissions of less than four tonnes of CO2 per tonne of aluminium – the lowest CO2 footprint in the world.
The global average is around 17 tonnes.
WORLD PRIMARY ALUMINIUM SMELTERS CARBON FOOTPRINT BASED ON ENERGY INPUT
ENERGY | TONNES CO2 PER TONNE OF ALUMINIUM |
---|---|
Hydro energy and renewable energy | < 4 tCO2/tAl |
Gas-powered energy | < 8 tCO2/tAl |
Combined hydro, wind, clean combustion coal | < 10 tCO2/tAl |
Mainly clean combustion coal | < 15 tCO2/tAl |
Combined coal and black Chinese coal | >17-20 tCO2/tA |
RECYCLING
Aluminium is capable of being recycled infinitely without losing its properties – and using a fraction of the energy required for producing primary aluminium. This makes it ideal for a ‘circular’ economy one in which products are manufactured from raw materials, used then repaired, re-used and recycled, reducing CO2 emissions and environmental impact compared to the linear economy of take, make and waste.
As such it is a vital resource for a climate-neutral and circular economy. Recycled aluminium currently accounts for about one-third of global consumption.
Around 75% of the almost 1.5 billion tonnes of aluminium ever produced is still in use today.
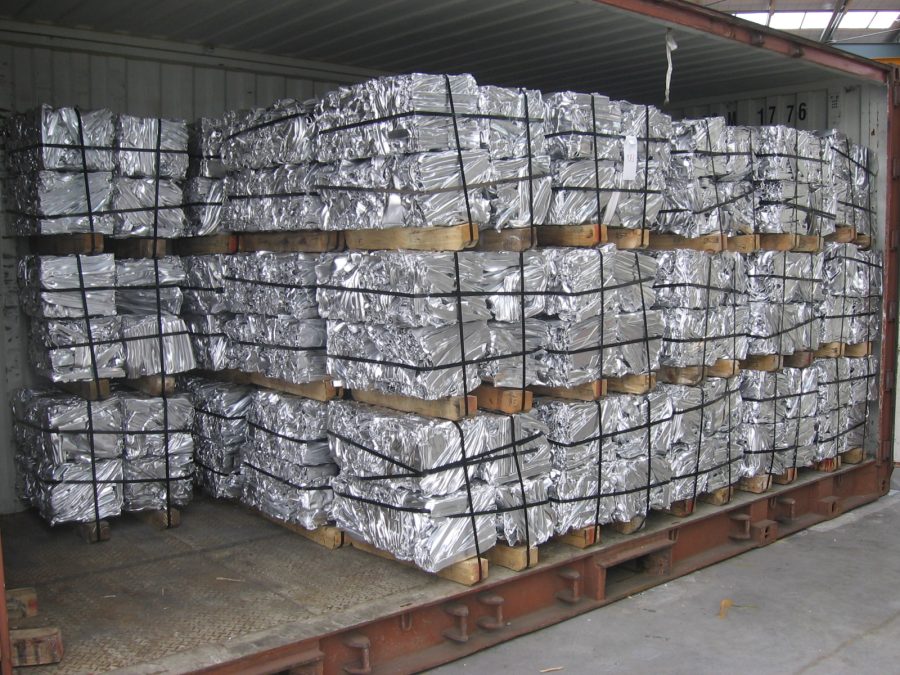
Recycling allows our industry to minimise waste, extract new value, reduce dependence on new aluminium – all further reducing our already low overall carbon footprint.
Our members are leaders in recycling.
• INEX is the only extruder in Australasia to recycle its scrap back to the primary producing smelter to produce aluminium billet, reducing energy needed in the manufacturing process without compromising high-quality. (Image left: INEX scrap being loaded into a casting furnace at the NZ Aluminium Smelter, Tiwai Point.)
• McKechnie is the only aluminium extruder in New Zealand to have a remelt, meaning its products have a high recycled content and a low carbon footprint.
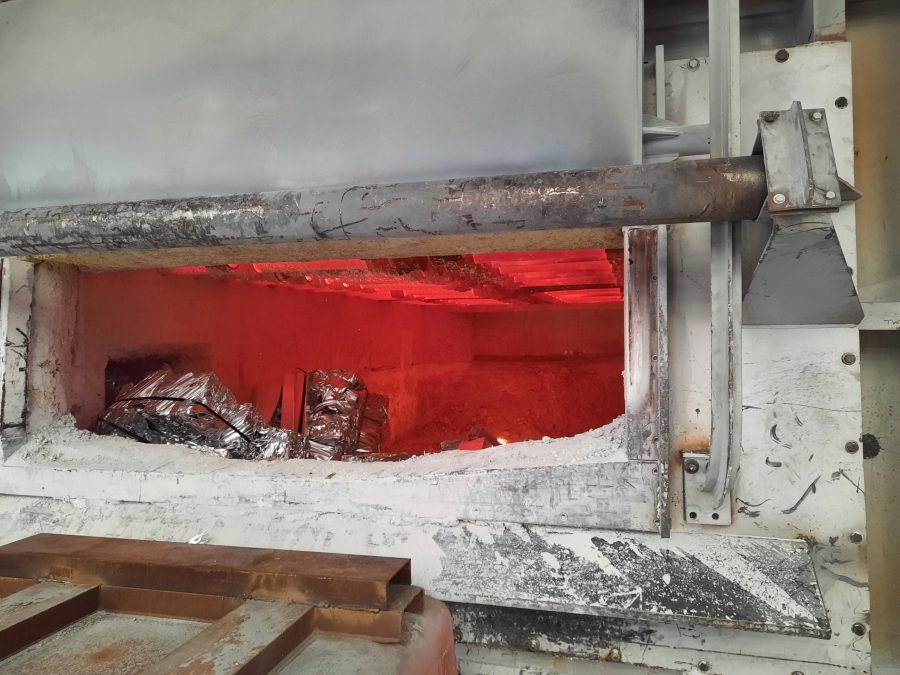
McKechnie has achieved a carbon footprint of 1.21kg of CO2e per Kg of aluminium on a Scope 1 and 2* basis, which is 90% better than the global average (11.5kg^ CO2e per kg of aluminium) CEMARS® third-party certified.

GOING GREEN GLOBALLY
New Zealand’s industry is well placed in a world where low-carbon materials are in high demand and high premiums are paid.
In Canada, carbon-free aluminium is already a reality with revolutionary new technology, ELYSIS™ that uses electrolysis to eliminate emissions from the smelting process and generate oxygen as a by-product.
ELYSIS is a partnership of two major aluminium industry pioneers – Alcoa and Rio Tinto – who are working to scale up and commercialise this new technology by 2024.
Whilst European Aluminium’s Circular Aluminium Action Plan aims to achieve aluminium’s full circular economy potential through a range of measures through the value chain including maximising decarbonisation and upscaling recycling.
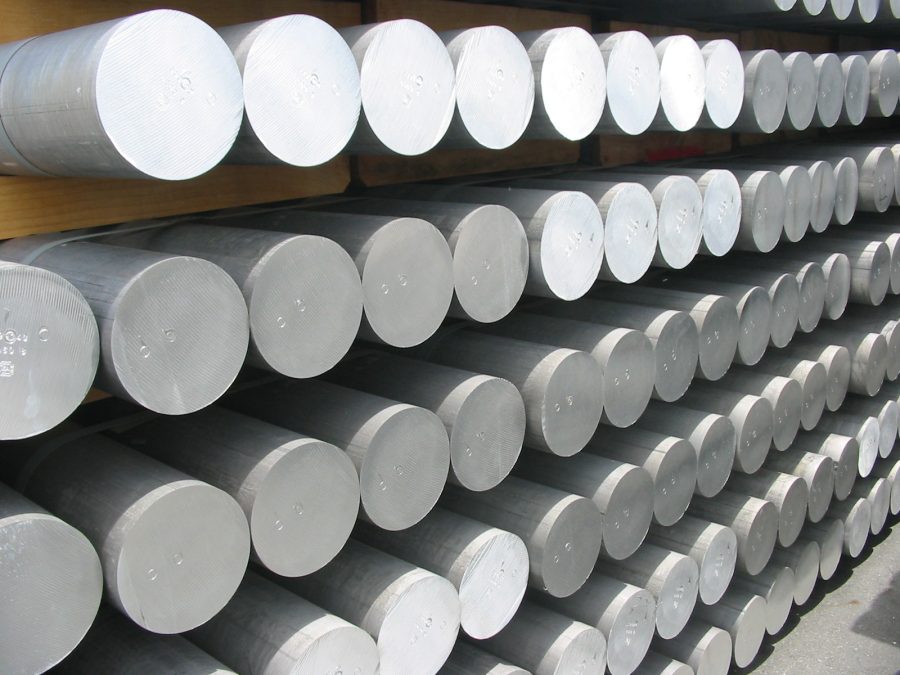